Chapter 9: SPF Case Studies
9.1 Case Study 1: Replacement of Flow Dividers in a Mining Facility
In a mining facility unit, there are 4 flow dividers operating. These items are not repaired, being replaced instead, and storage for these items was too arbitrary, not based on any metric. The problem is that the spare items are bought only once per year, and sometimes the stock is lacking new flow dividers.
When there are no available spare items in stock, unfortunately, there is no way to buy new dividers, and the facility must wait until next resupply date, or order spare ones from other mining stations, which can take up to one month.
Having information on a previous LDA performed on these assets, for a Weibull distribution, the parameters were 1.4213 for beta and an eta of 6.7911 months.


The results point that, when having over 16 flow dividers in stock, the total cost starts to converge to the cost of acquiring the new items, and the cost due to profit loss for shutting down the line is getting to a point where it causes minimum concern.

9.2 Case Study 2: Truck Brake Pads – Part 2
A company that uses the same trucks made by the manufacturer mentioned on the 3.2 Case Study, present on the Degradation Analysis Case Studies (Chapter 13), is making a maintenance strategy for the running trucks in the field. Along with other data regarding the lifespan of the truck’s parts and systems, they asked for the brake pads LDA parameters, which were already obtained by the Degradation Analysis made previously on Chapter 3.
The Weibull Reliability Plot for the pads, sent by the manufacturer (figure below) displays the parameter values on the bottom.

On the field, there are 30 trucks running on the field. They operate for about 12 hours daily, and they cover, in average, 720 kilometers per day. When the brake pads need replacement, a truck stays on the center for about one whole day, and the profit loss due to that is equivalent to 170 dollars for the company, in average.
They resupply new brake pads every 150 days, and, as each truck has 8 wheels and each wheel has a brake pad, there are a total of 960 brake pads on the running vehicles.

Important Note: As the parameters were estimated for mileage, we are expressing the eta parameter in days, which is possible since there is the information that the trucks run approximately 720 kilometers per day. Assuming that there is little deviation from this value, beta is not affected, however, every other data required in the analysis must also be expressed in days.

The results point out that the lowest total cost is reached upon having 95 spare pads in storage:
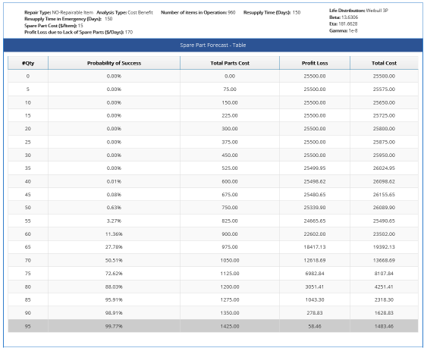

So, for a cost benefit priority, every time this company resupplies for these pads, they must have in mind that they need to maintain 95 units in storage.